GMP Vs Toyota's TPS - Manufacturing Excellence
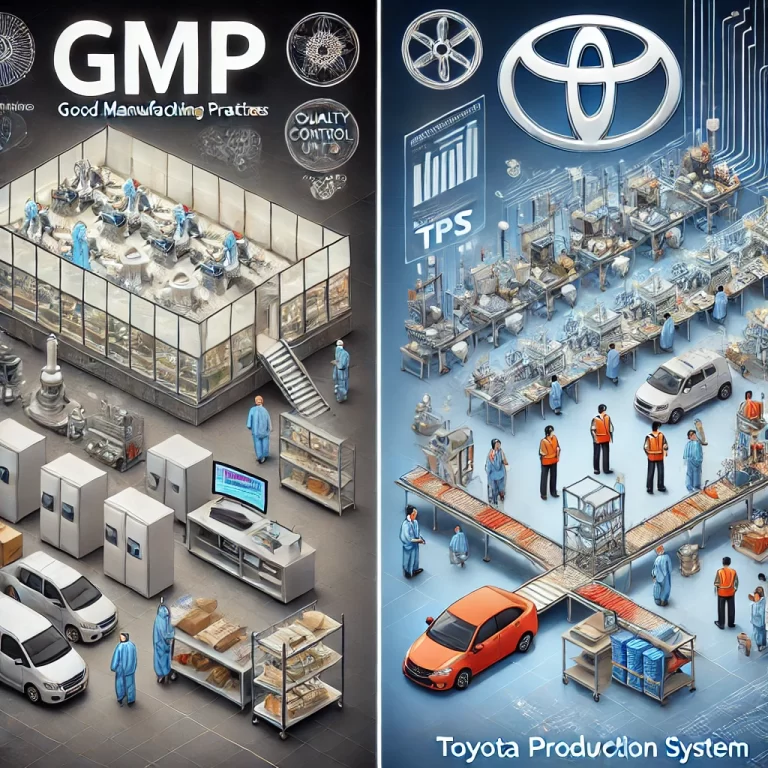
Manufacturing Excellence: Driving Innovation, Quality, and Efficiency
Excelling, in Manufacturing. Enhancing Innovation and Efficiency, with Quality
In todays changing economy manufacturing excellence is more, than just a goal—it’s a vital requirement. Businesses that excel in manufacturing distinguish themselves by efficiently and consistently producing top notch products in a manner. Manufacturing excellence involves principles, methods and techniques focused on enhancing production processes maintaining quality standards and reducing waste.
Achieving excellence, in manufacturing involves following Good Manufacturing Practices (GMP) and implementing industry leading strategies like the Toyota Production System (TPS) known for its quality lean manufacturing approach worldwide. In this blog post discussion revolves around the significance of manufacturing excellence along with GMP adherence and the positive impact of Toyotas methodologies, on achieving manufacturing excellence.
What does Manufacturing Excellence entail?
The pursuit of manufacturing excellence entails a method to production that prioritizes enhancement and effectiveness through innovation and efficiency efforts across all stages of the manufacturing process to boost output quality while cutting costs and waste levels significantly while emphasizing value creation, for the company’s stakeholders and customers as integral objectives, alongside employee satisfaction and welfare considerations.
In fields, like technology and electronics as well as in pharmaceutical and food industries among others alike this idea is relevant and widely applicable, with a common objective. To enhance operational productivity without compromising on product excellence.
“The Core of Manufacturing Excellence lies within the Toyota Production System.”
The Toyota Production System (TPS) stands out as an illustration of manufacturing prowess and innovation, due to its commitment, to streamlining operations and promoting efficiency while upholding top notch product standards.
Toyotas strategy is centered on two foundations;
Just, in Time ( JIT ) Production strategy ensures that items are made precisely when necessary and, in the amount needed to decrease surplus stock levels and minimize inefficiencies while maximizing resource utilization.
“Embracing Jidoka (Automation, with a Human Touch) involves creating systems and machinery that can halt operations automatically upon detecting issues to prevent defects from advancing along the manufacturing line effectively empowering workers to halt production in case of quality concerns and fostering a culture centered on quality.”
These fundamentals work hand in hand to uphold the foundation of TPS and empower Toyota to excel in manufacturing through minimizing waste and striving for enhancement of quality control practices.”
Essential Foundations of Manufacturing Excellence.
Becoming a manufacturing powerhouse, like Toyota entails following a organized strategy that addresses essential aspects of the process.The fundamental elements that contribute to manufacturing greatness are as follows;
Efficient Manufacturing
The concept of manufacturing revolves around getting rid of inefficiencies and enhancing productivity by cutting down waste in forms such, as overproduction and excessive inventory – key principles underpinning the Toyota Production System that many manufacturers adopt to streamline their operations effectively and boost output.
Toyotas efficient methods are based in the quest, for enhancement known as Kaizen—an ideology that motivates staff members at every level to pinpoint inefficiencies and propose enhancements to procedures.This grassroots method guarantees that lean practices become a part of the organizations ethos and that advancements are continuous.
Six Sigma methodology is an approach used in quality management.
Lean manufacturing centers, on waste reduction while Six Sigma is a methodology that targets decreasing variability in processes to enhance quality standards.The amalgamation of Lean and Six Sigma known as Lean Six Sigma offers a strategy for attaining manufacturing superiority by tackling efficiency and quality, in harmony.
Toyota pays attention to quality by being very careful and thorough, in their approach to preventing errors through techniques like Poka Yoke and align, with the Six Sigma philosophy of minimizing defects to zero.
Advancements, in technology and creativity
In the era of Industry 4.O. it is essential for manufacturing success to prioritize innovation and technology integration.Toyota has adopted advancements by integrating factories with cutting edge technologies such, as automation,A.I. And Internet of Things (IoS) all aimed at enhancing production efficiency.
These tools help Toyota gather and analyze data instantly to anticipate equipment malfunctions and enhance maintenance plans while minimizing delays.Through the use of data and technology advancements Toyota strives to maintain standards, in efficiency and quality, within its manufacturing operations.
Ensuring quality standards and compliance, with Good Manufacturing Practices (GMP)
Manufacturing excellence thrives on quality standards. Toyota is widely recognized for its dedication to this principle. Effective Quality Management Systems ( QMS ) play a role, in enabling businesses to deliver products that not meet but surpass customer expectations. Toyotas focus on Jidoka guarantees that quality control is integrated at each stage of the manufacturing process.
Companies not have to follow industry standards but also comply with Good Manufacturing Practices (commonly known as GMP) in sectors such, as pharmaceuticals and cosmetics where product safety is importance ensuring regulatory compliance and maintaining high product quality and safety standards are prioritized by sticking to GMP regulations.
Understanding Good Manufacturing Practices (GMP)
Good Manufacturing Practices (GMP) are a set of regulations and guidelines designed to ensure that products are consistently produced and controlled according to quality standards. These practices are essential in industries where product quality and safety directly impact consumers’ health.
GMP ensures that facilities, equipment, personnel, and processes are optimized to maintain high standards of sanitation, hygiene, and quality control.
- Personnel and Training
GMP emphasizes the need for well-trained personnel who are knowledgeable about hygiene practices, quality standards, and safety protocols. Toyota’s focus on employee empowerment through the Kaizen philosophy mirrors this by encouraging workers to be proactive in improving processes and ensuring quality.
- Facilities and Equipment
In both GMP and Toyota’s system, maintaining clean, well-functioning facilities and equipment is crucial to ensuring high-quality production. Regular maintenance and inspections ensure that equipment operates optimally and that production lines run efficiently, minimizing downtime.
- Documentation and Record-Keeping
GMP requires meticulous documentation of every stage of the production process. Toyota’s system is similarly data-driven, with a focus on tracking processes and maintaining transparency in production.
- Sanitation and Hygiene
GMP places a high priority on cleanliness and hygiene to prevent contamination. Toyota’s emphasis on 5S methodology (Sort, Set in Order, Shine, Standardize, Sustain) in the workplace ensures a clean, organized, and efficient production environment, aligning with GMP’s focus on sanitation and quality.
The Benefits of Implementing GMP and Toyota Practices
By integrating GMP with Toyota’s production principles, companies can ensure that their manufacturing processes are not only efficient but also produce high-quality, safe products. The benefits include:
– Compliance with Regulations: GMP ensures compliance with industry regulations, reducing the risk of fines, penalties, or recalls.
– Improved Product Quality: Toyota’s focus on Jidoka and error-proofing aligns with GMP’s goal of consistent product quality.
– Increased Efficiency: Lean practices, such as Just-in-Time production, reduce excess inventory and streamline processes, leading to greater efficiency.
– Enhanced Reputation: Companies that follow Toyota’s practices and adhere to GMP build trust with customers, stakeholders, and regulators.
My Conclusion: Toyota as a Model of Manufacturing Excellence
Manufacturing excellence is about more than just producing goods—it’s about delivering value through efficiency, quality, and continuous improvement. Toyota’s approach to manufacturing, built on lean principles, Just-in-Time production, and Kaizen, serves as a model for achieving excellence in today’s competitive marketplace.
By integrating best practices like GMP and adopting the principles of Toyota Production System, companies can enhance their operational efficiency, ensure product quality, and maintain a culture of continuous improvement. In a world where consumer expectations are rising and competition is fierce, manufacturing excellence is key to long-term success.
This blog tries to integrate Toyota’s lean manufacturing philosophy, highlighting how their principles, alongside GMP, can drive manufacturing excellence in modern industries.
Bonus
Here are 5 interesting facts about Toyota:
- Birth of the Name “Toyota”
The company was originally called Toyoda, after the family name of its founder, Kiichiro Toyoda. However, in 1936, the name was changed to Toyota because writing it in Japanese required eight strokes, a number considered lucky in Japanese culture.
- Pioneers of Lean Manufacturing
Toyota developed the Toyota Production System (TPS), which revolutionized modern manufacturing by introducing concepts like Just-in-Time (JIT) and Kaizen (continuous improvement). These practices have been adopted globally and form the basis of Lean Manufacturing.
- The First Mass-Produced Hybrid Car
Toyota introduced the world’s first mass-produced hybrid car, the Prius, in 1997. It became a global success and positioned Toyota as a leader in environmentally friendly technologies.
- The Largest Car Manufacturer
As of recent years, Toyota is one of the largest car manufacturers in the world by sales volume. In 2020, Toyota sold over 9.5 million vehicles, surpassing Volkswagen to become the world’s top automaker.
- Toyota’s Global Reach
Toyota operates in more than 170 countries and produces vehicles in 28 countries. Its global footprint ensures that it caters to diverse markets with localized production and products tailored to different regions.
Here are some External Links for your reference: –
Links for GMP (Good Manufacturing Practices):
- FDA: Good Manufacturing Practices (GMP) Regulations – FDA GMP Overview- https://www.fda.gov/drugs/pharmaceutical-quality-resources/current-good-manufacturing-practice-cgmp-regulations
This page provides detailed information about GMP regulations, particularly in the pharmaceutical industry, outlining the importance of quality control and regulatory compliance.
- WHO: Good Manufacturing Practices (GMP) – WHO GMP Guidelines- https://www.who.int/teams/health-product-policy-and-standards/standards-and-specifications/gmp
The World Health Organization (WHO) offers comprehensive guidelines on GMP for ensuring product safety and quality in the pharmaceutical sector.
- International Society for Pharmaceutical Engineering (ISPE): GMP Overview – ISPE GMP Overview – https://ispe.org/initiatives/regulatory-resources/gmp
The ISPE site provides insights into GMP practices and how they relate to improving manufacturing excellence and product integrity in regulated industries.
Links for Toyota Production System (TPS):
- Toyota Global: The Toyota Production System – Toyota Global TPS Overview – https://global.toyota/en/company/vision-and-philosophy/production-system/
Toyota’s official page explaining the principles of the Toyota Production System (TPS), including lean manufacturing, just-in-time production, and continuous improvement.
- Lean Enterprise Institute: Toyota Production System – Lean Enterprise TPS – https://www.lean.org/lexicon/toyota-production-system
This page explains the Toyota Production System and how lean manufacturing practices derived from TPS can improve efficiency and reduce waste in various industries.
- Toyota UK: How Toyota’s Production System Works – Toyota UK TPS – https://blog.toyota.co.uk/how-the-toyota-production-system-works
This blog provides an easy-to-understand breakdown of Toyota’s Production System and its core pillars, such as kaizen (continuous improvement) and jidoka (automation with a human touch).
General Links on Manufacturing Excellence:
- Harvard Business Review: Lean at Wipro—Lean Techniques in Service
HBR Lean at Wipro – https://hbr.org/2007/11/lean-at-wipro-technologies
An example of how lean manufacturing principles, similar to Toyota’s TPS, are being applied in service industries to enhance operational excellence.
- McKinsey: The Next Level of Operational Excellence in Manufacturing
McKinsey Manufacturing Excellence – https://www.mckinsey.com/business-functions/operations/our-insights/the-next-level-of-operational-excellence-in-manufacturing
McKinsey discusses how manufacturers can achieve operational excellence through advanced techniques, including the implementation of GMP and lean systems like TPS.