The 7 QC Tools What are They and Why Use them
(2024 Updated)
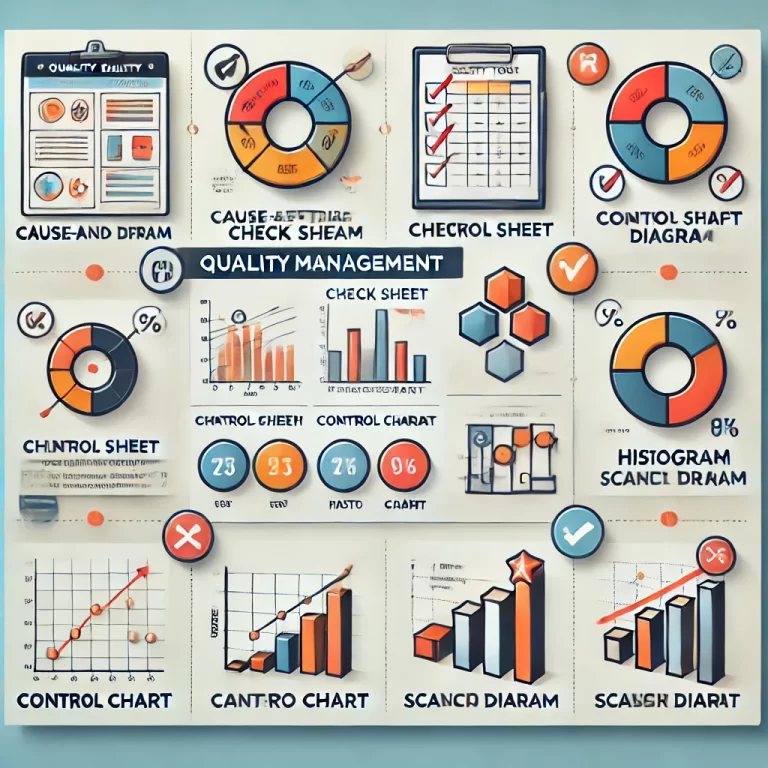
THE WHY WHAT WHEN WHERE & HOW OF IT
The 7 Quality Tools are commonly known as the “Seven Basic Tools of Quality”. Play a role, in maintaining and enhancing quality across different sectors of industry. They were made famous by Kaoru Ishikawa who advocated for their simplicity and effectiveness in addressing a portion of quality issues within companies. These tools serve as the building blocks, for management Six Sigma and Total Quality Management (TQM) supporting decision making based on data and driving enhancements in processes. Let’s take a look, at all seven tools.
LOOKING FOR A TRAINING PROGRAM ON THIS SUBJECT
DEALS THAT YOU CANNOT MISS THIS SEASON
- Fishbone Diagram (also known as Cause-and-Effect Diagram)
The Ishikawa or Fishbone Diagram is a tool that visually illustrates the reasons, behind a problem or defect to assist teams, in potential sources of issues in an organized way.
The illustration looks like the frame of a fish, with the “head” representing the issue and the “bones” symbolizing causes categories such, as Manpower, Methods Machines, Materials, Measurement and Environment.
This tool is perfect for pinpoint the reasons, behind issues in manufacturing and service operations well, as other processes. It helps with brainstorm and sorting out causes which allows teams to tackle problem solving in a thorough manner.
- Check Sheet
A checklist is, like a form that’s organized for collecting and analyzing data. Usually looks like a tally chart of sorts! It helps teams collect both numbers and descriptions, about happenings or issues so they can spot trends and patterns easily.
The format of inspection forms is simple and can be tailored to match the data being gathered; for example, they might record the kinds of faults observed and how often they happen well as when and where they occur.
Sheets, for checking are often utilized to document how often particular problems occur like defects in manufacturing or errors, in service procedures. This information can then guide analysis and efforts to enhance quality.
- Control Chart
Control charts, developed by Walter A. Shewhart, are graphical tools used to monitor process stability and control over time. They plot data points against upper and lower control limits to help identify variations.
The chart typically includes a central line representing the process average, with upper and lower control limits set based on statistical analysis. Data points that fall outside these limits indicate potential out-of-control conditions.
Control charts are critical for maintaining process control in manufacturing, service delivery, and any process where consistency is crucial. They help identify special causes of variation, allowing corrective actions to be taken before issues impact quality.
- Histogram
A histogram is, like a graph with bars that display how data is spread out by showing how often certain value ranges appear in a dataset. It’s useful for spotting trends, in data and understanding how processes work and vary.
The horizontal line shows the sets of information (sometimes referred to as bins). The vertical line displays how often each set occurs within a specific range.
Histograms are commonly utilized in quality enhancement to comprehend data distribution and diversity effectively. They play a role, in recognizing if data follows a pattern or shows skewness or the presence of outliers that might suggest underlying process concerns.
- Pareto Chart
In a Pareto chart you’ll see a bar graph illustrating how 80 percent of problems typically stem from 20 percent of causes also known as the Pareto Principle. This chart assists in prioritizing concerns by highlighting the causes that have the impact.
The graph displays bars that indicate either frequency or cost in a descending arrangement alongside a line graph demonstrating the percentage accumulated far.
Teams can effectively focus their problem-solving efforts, on issues. Enhance the quality improvement impact by utilizing a Pareto chart tool to prioritize tasks based on importance. This method proves valuable in pinpoint defect categories. Cost drivers and, in recognizing prevalent customer complaints.
- Scatter Diagram
When you look at a scatter diagram or scatter plot visually you can see how two variables relate to each other and figure out if there’s a connection, between them.
Each mark, on the graph indicates an observation placed on the variable) and vertical (dependent variable) axes. Various patterns, like going up going down or showing no trend can indicate kinds of connections.
Scatter plots are handy, in quality control for examining relationships, between causes and effects; for example, they can aid in pinpoint whether specific machine configurations are linked to product flaws and allow for accurate tweaks to be made.
- Flowchart
A flowchart serves as a depiction of a procedure by illustrating each stage from commencement to conclusion; it aids in outlining the order of activities and decision nodes along, with routes, within a procedure.
Flowcharts utilize symbols, like circles for starting or ending points. Rectangles, for procedural steps to represent a process in a clear and organized manner.
Flowcharts are incredibly useful, in pinpointing inefficiencies and redundancies within processes. Also help in identifying bottlenecks. They play a role in training programs and process documentation while being a tool in analyzing intricate workflows in various sectors, like manufacturing, services and administrative roles.
Implementing the 7 Quality Tools for Effective Problem-Solving
The seven Quality Tools work best when combined in a manner as part of an enhancement plan, for quality standards integration, into improvement procedures;
Lets begin by outlining the issue using a Fishbone Diagram to explore causes and then use a Check Sheet to collect data related to those causes.
Examine Data Analysis, by utilizing a Histogram to comprehend the distribution of data and a Pareto Chart to pinpoint the concerns.
Ensure you have control in place by utilizing control charts to keep track of process stability and employ scatter diagrams to explore correlations, between variables.
Enhancing Procedures; Flowcharts play a role, in outlining enhancements and streamlining procedures to steer teams, towards a smoother workflow.
Benefits of Using the 7 Quality Tools
Tools, for data driven decision making individuals to make choices grounded in data rather, than mere assumptions; this approach minimizes uncertainty and enhances the dependability of decisions made.
Improved Ability to Solve Problems Effectively; Teams can tackle quality problems at their origin by pinpointing reasons examining patterns and gauging fluctuations, in data.
Enhanced Productivity and Client Contentment; These tools aid, in lowering mistakes and cutting down on waste while boosting the efficiency of processes overall for improved product or service quality.
Having a culture of improvement involves using these tools to create an environment focused on quality and enhancements within a company. This approach makes it simpler to adjust to shifts and strive for excellence.
In summary
The 7 Quality Tools play a role, in quality management by offering adaptable approaches to analyze and enhance processes effectively. They help organizations manage process variations efficiently and make informed decisions based on data to maintain levels of quality and productivity. These tools are versatile across industries and aid, in driving improvements while fostering a culture of ongoing quality enhancement.
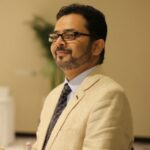
Syed Saif has over two decades of experience in Quality, Excellence, Innovation, Six Sigma, Lean, and Customer Services. He is a Certified Master Black Belt, ISO Lead Auditor, High Impact Trainer, Certified Business Excellence Assessor, Certified on Innovation Business Model Canvas, and holds a PG diploma in Customer Relationship Management. Syed Saif founder of Brainow Consulting and has trained thousands of people, across industries from students to CEOs on various improvement methodologies and self help techniques. He has worked in various industries including BPO, Telecom, IT, Insurance, Manufacturing, and Healthcare. Prior to this full-time consulting role, he served as Vice President for a Leading Insurance Company and as National Head of Quality, Innovation, and Service Excellence for Corporate and Sales Functions. See our services page for more details on what we do and how can we help you / your organization.